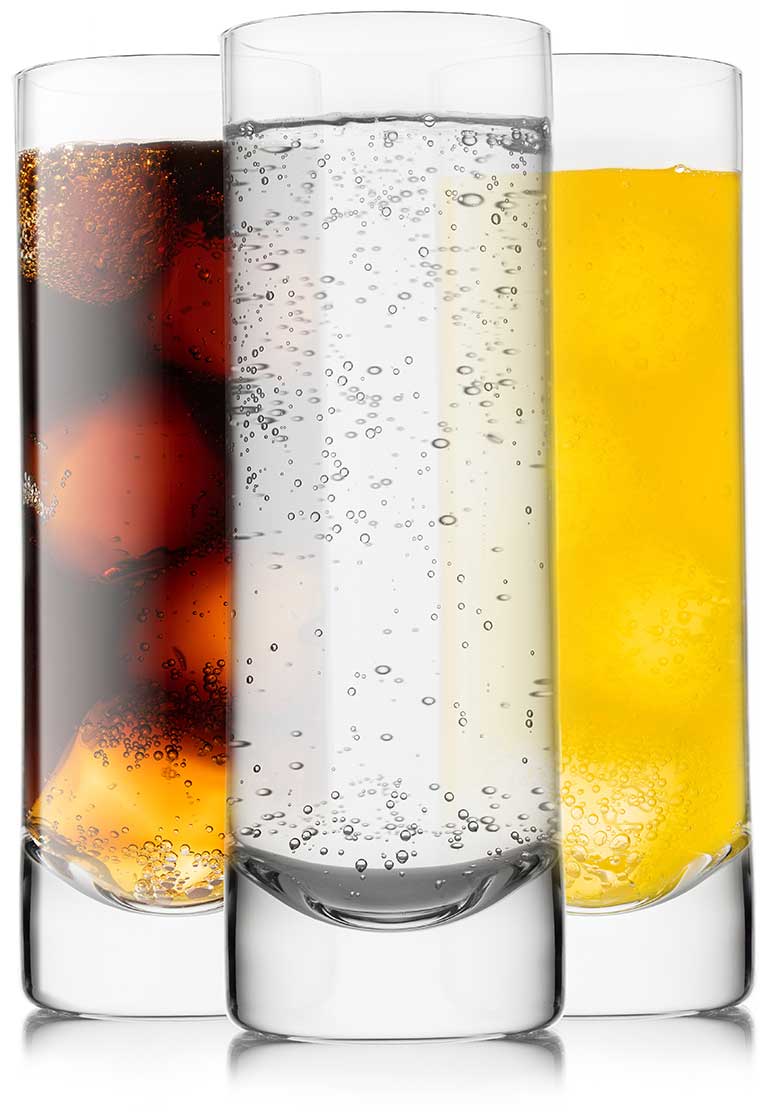
Challenges for the beverage industry
In addition to the need to ensure efficient, resource-conserving and sustainable production, the beverage industry faces ever-increasing energy and raw material costs. Energy costs, in particular, pose a significant burden, as many production process steps (mixing, cooling, aerating, conveying, filling, palletizing) are very energy intensive. Furthermore, the demand for packaged products continues to rise despite numerous sustainability measures, and consumers increasingly expect individualized offerings. All this is placing added pressure on manufacturers to provide a diverse range of products while also adhering to stringent standards and norms.
Overcoming these complex challenges necessitates innovative approaches and solutions to maintain competitiveness and achieve sustainability goals.
- Rising energy and raw material costs
- Sustainability
- Stringent statutory regulations
- Consumers expecting increasingly extensive product ranges
- Shortage of labor
Thanks to our over 37 years of experience and high-performance automation solution Plant iT, we are the ideal partner for all beverage manufacturers seeking to overcome these challenges. Plant iT provides the foundation for a sustainable competitive edge and helps develop your future readiness.
Trend-setting solutions for the beverage industry
Leading manufacturers in the beverage industry are investing in automation solutions to address the aforesaid challenges and to achieve lasting competitive advantages. Are you looking for a solution for your production plant that:
- facilitates your processes,
- optimizes your entire value-added chain,
- increases the productivity, flexibility and sustainability of your business,
- helps make your business more profitable
- and accompanies you on your journey to building the industry of the future?
Plant iT is our established automation solution designed to meet your needs and is specifically tailored to the demands of the beverage industry.
The object-related, PLC-based process control system developed by ProLeiT GmbH, including MES functionality, caters to both the general and the specific requirements of the beverage industry. Plant iT can be used in combination with PLCs from various manufacturers and is available in more than five language versions.
More than 250 installations
in 110 countries worldwide
Success stories from our customers and partners
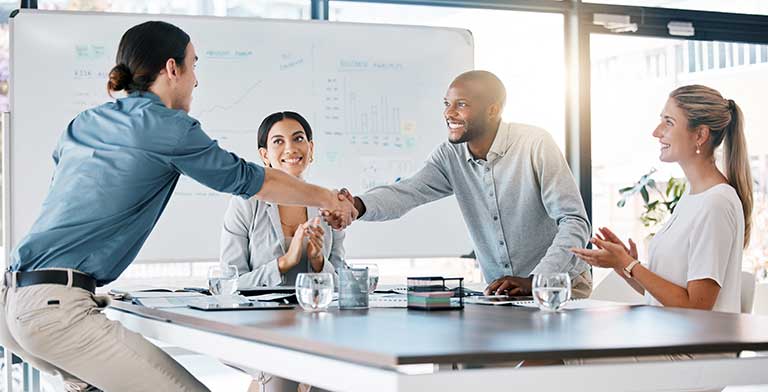
For over 37 years, ProLeiT has proudly fostered partnerships with leading manufacturers in the beverage industry. The joint completion of projects inspires us daily to further shape the future of automation. The close exchange with our customers and the mutual enrichment of our experiences are paramount to us. The more than 250 installations worldwide attest to our reliability and the trust vested in us.
Discover the world of our customers
Explore our collection of fascinating customer stories and draw inspiration from the successes of our well-known references.
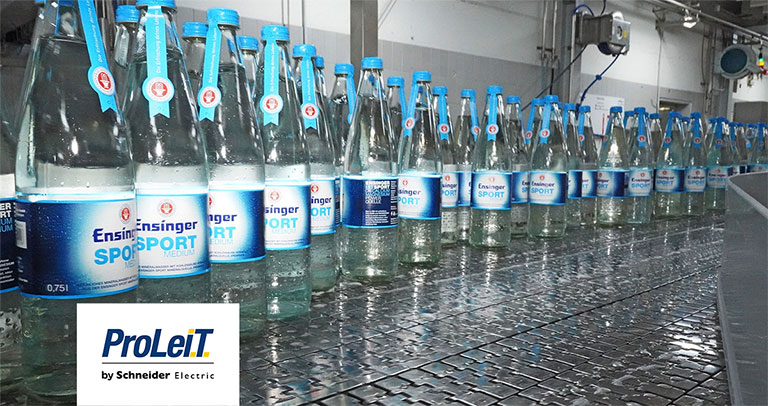
Ensinger
Ensinger Mineral-Heilquellen GmbH has been producing mineral water since 1952. The Plant iT process control system from ProLeiT automates production. The renewed partnership was swiftly established to bridge the gap between the shop floor and the commercial level.
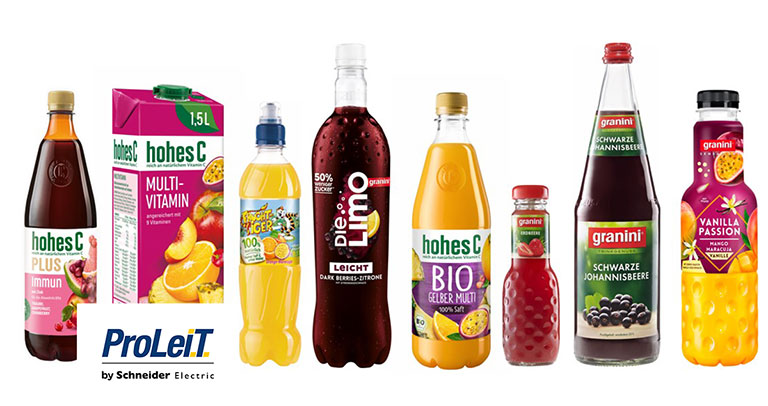
Eckes-Granini
Digitalization is taking shape. This also applies to Eckes-Granini Deutschland GmbH, which has been cooperating with ProLeiT in the field of process control technology since 2012. Discover how Eckes-Granini benefits from continuous energy data acquisition with horizontal and vertical integration thanks to ProLeiT.
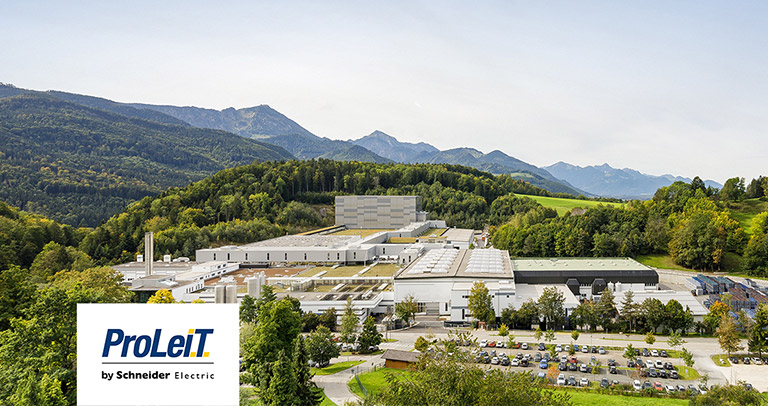
Adelholzener
Through the adoption of the Plant Batch iT process control system, Adelholzener Alpenquellen is enhancing its syrup production - from handling residual quantities to integrating scanners and interfacing with the MES solution.
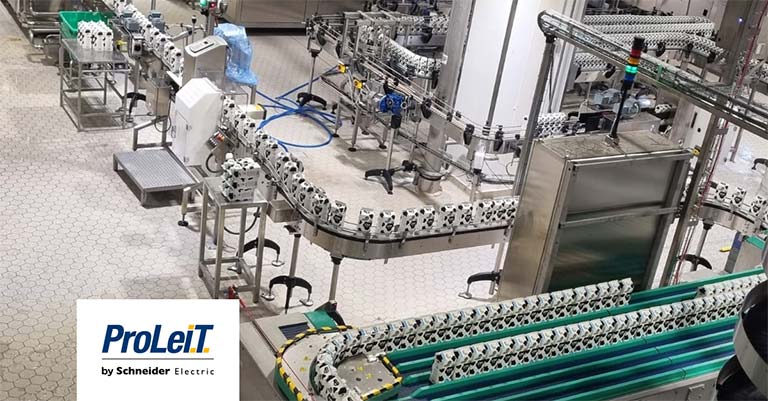
Tara
More efficiency, long-term update capability and fit for the future in terms of cybersecurity: Discover how ProLeiT upgraded the process control system at Tara, a long-standing dairy customer, in just 24 hours.
Our customers
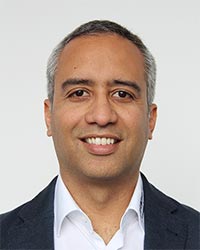
Your contact for the beverage production of the future
Hernán Alvarado
Branch Leader
Beverages
Phone: +49 162 2598 184
E-mail: hernan.alvarado(at)proleit.com
Plant iT - the automation solution for the beverage industry
With its proven track record of success, Plant iT is the ideal automation solution for the beverage industry. It offers seamless integration across all processes from goods receipt to filling. Moreover, it enables efficient horizontal and vertical integration. Supported by our in-house system development team and close cooperation with renowned beverage manufacturers, plant suppliers and universities, Plant iT provides a cutting-edge process control system for the beverage industry.
By the way: If you are looking for automation solutions for breweries, we highly recommend our industry-specific solution brewmaxx! Like no other process control system on the market, brewmaxx is perfectly tailored to the day-to-day needs of breweries.
Current product highlights
Discover a world full of innovation and progress. With Plant iT, you are always one step ahead when it comes to the latest solutions for beverage manufacturers. Our in-house research and development team continually works on enhancing our innovative product portfolio.
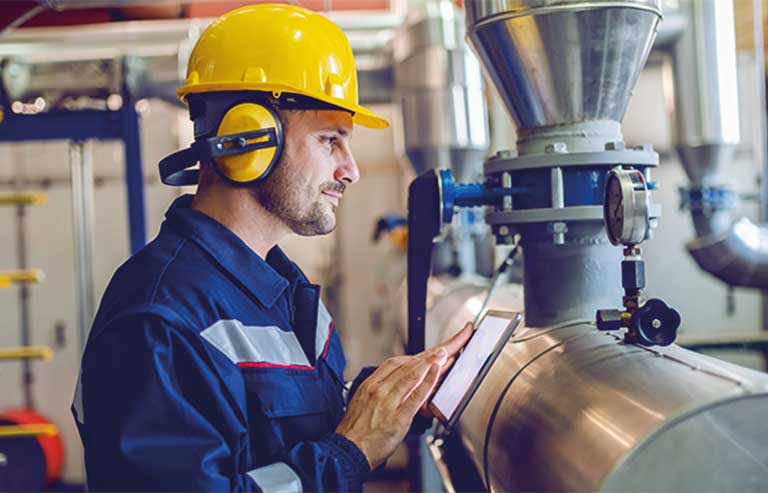
Recipe management for batch processes
Do you want to process multiple production orders for different products simultaneously? No problem for Plant Batch iT, our central process control system for controlling and monitoring recipe-controlled batch processes.
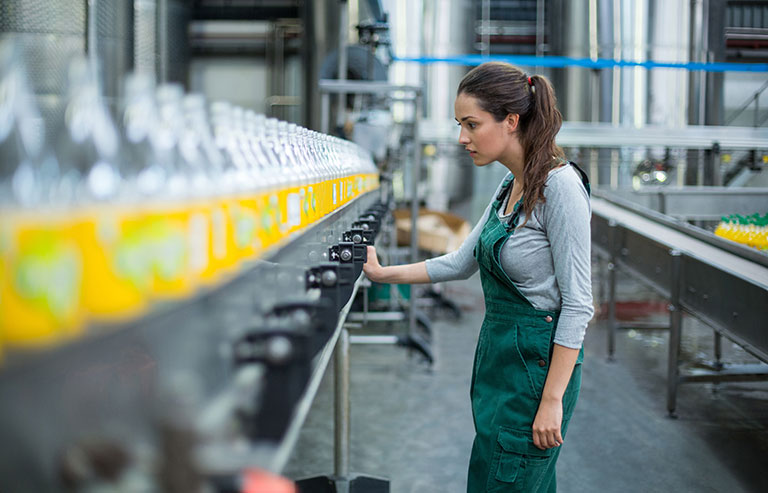
Line Management System
Minimizing downtime and maximizing plant efficiency - our Plant Acquis iT LMS add-on automatically, reliably and precisely records plant and machine downtime and ensures easy entry into the world of line management.
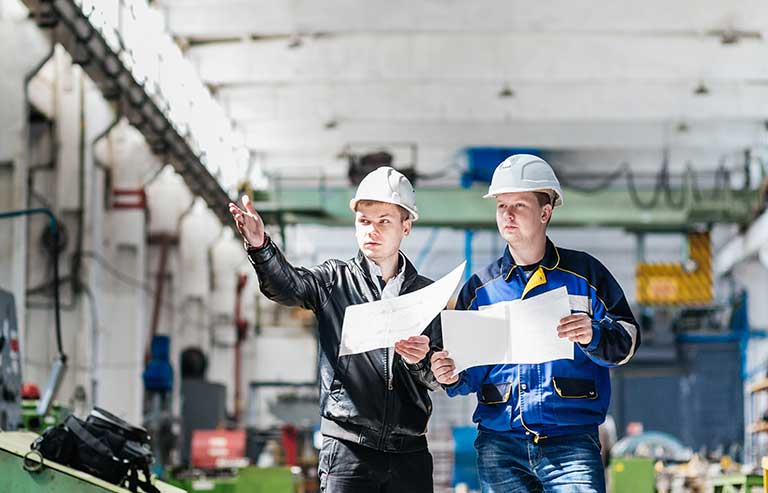
Workflow Management
Our high-performance MES Workflow Management system Plant iT Workflow assists you in managing and monitoring both automatic and manual processes in the production environment, including areas such as order processing, quality assurance and logistics.
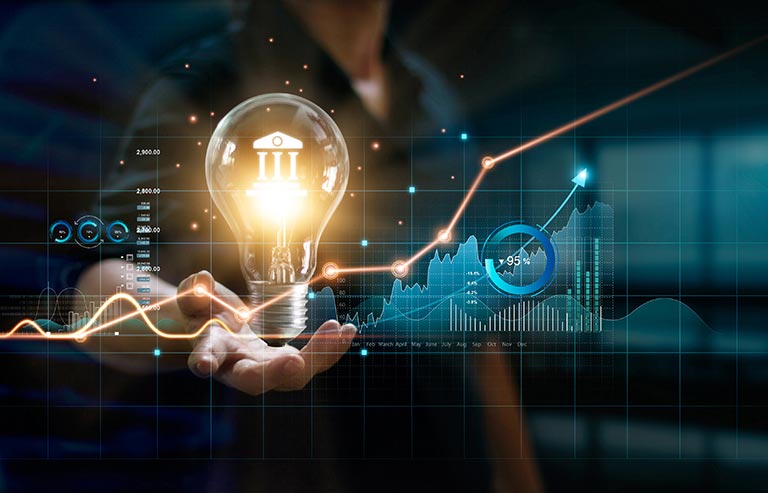
Energy Management
Efficiently monitor and control energy consumption in your plant with our Energy Management system. Identify optimization potential and improve the long-term energy efficiency of your beverage production.
Take a look at the many added values Plant iT offers
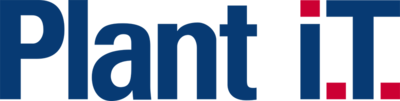
Plant iT is the modular process control system from ProLeiT GmbH and has been deployed throughout the process engineering industry in more than 110 countries for over 37 years. From operating data acquisition, process control technology, liquid handling and batch systems to functions for complete, location-independent production management (MES) and integration of ERP, LIMS and maintenance systems – Plant iT enables continuous control and monitoring of all these processes.
Thanks to a central engineering environment and optional modules, Plant iT can be expanded flexibly to meet various needs. Plant iT complies with the principle of "parameterization instead of programming". This means that individual programming is essentially replaced by the parameterization of technical and technological functions. Plant iT's system architecture offers maximum flexibility for changes, even during production, without the need to shut down operations. This time-saving approach offers our customers a distinct competitive advantage.