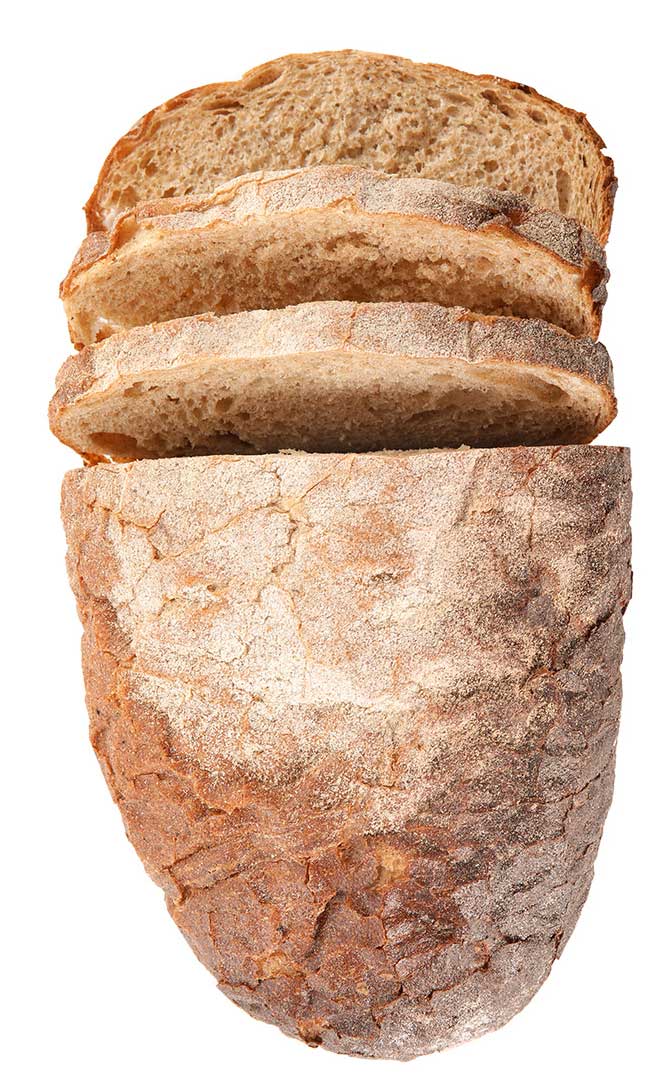
Challenges for the baking industry
The baking industry is facing a variety of challenges in the present landscape. These challenges encompass rising expectations for product quality and safety, the need for more sustainable production methods and packaging solutions and the necessity to align with evolving consumer trends and nutritional regulations. Furthermore, the manufacturers of baked goods must ensure efficient production processes while simultaneously responding to surges in raw material prices and supply chain disruptions.
Within large industrial bakeries, production lines often comprise a myriad of systems and machines from various manufacturers, which have little or no communication with each other. When facilities produce convenience and frozen products alongside standard baked goods, typically both the list of suppliers and the number of systems and machines expand. This diverse array of plants and machinery is segmented into numerous process areas and is seldom fully automated or integrated into an overarching IT system.
Numerous plant and machine manufacturers provide information solutions in the form of SCADA systems. Yet these systems are often restricted to their own plants and specific process areas, rather than being designed for a production line or the entire production facility. The need for a higher-level process system becomes apparent when considering existing dispatching, storage and logistics systems, or when producing pastries.
Innovative solutions for an integrated bakery of the future
Increasing product diversity and mounting cost pressure: Achieving success in the bread and baking industry necessitates a flexible automation solution. Are you currently facing the aforesaid challenges and looking for a solution that:
- facilitates your processes,
- optimizes your entire value-added chain,
- increases the productivity and flexibility of your business,
- helps make your business more profitable
- and accompanies you on your journey to building the industry of the future?
Our Plant iT control system presents the ideal solution. Regardless of existing systems and requirements, Plant iT can process information from all process areas and undertake integrated process management through defined interfaces.
Thus, Plant iT can ensure adherence to recipe specifications for quality compliance, calculate material consumption based on the order list and guarantee comprehensive traceability of the entire production process in accordance with statutory regulations.
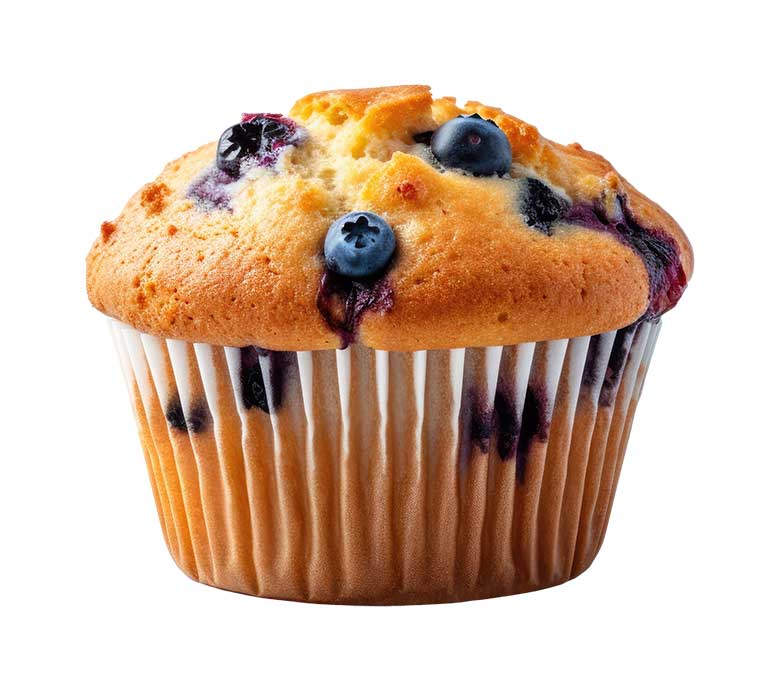
Success stories from our customers and partners
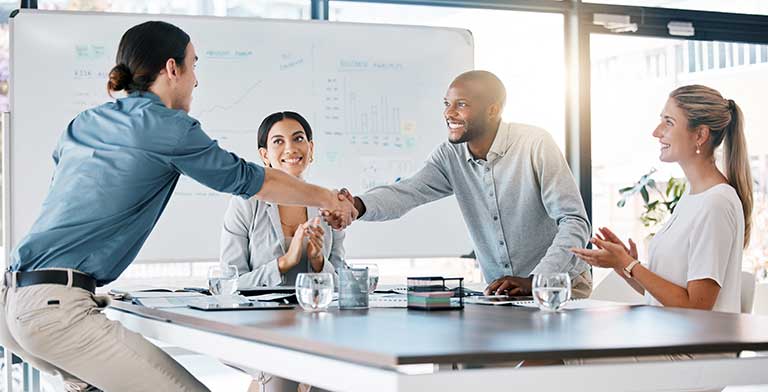
ProLeiT takes pride in its over 37 years of collaboration with esteemed customers in the bakery sector. The successful completion of joint projects inspires us to continue shaping the future of automation daily. We value the personal interaction with our customers, the exchange of professional insights and the mutual enrichment of our experiences. We engage in intensive dialog with universities, dairy associations and institutes, fostering knowledge transfer in process control technology, automation and MES solutions. A prime example of this is our successful cooperation with the Technical University of Munich (TUM).
Learn more about ProLeiT customers
Discover our archive of fascinating customer stories and be inspired by the success of our well-known testimonials.
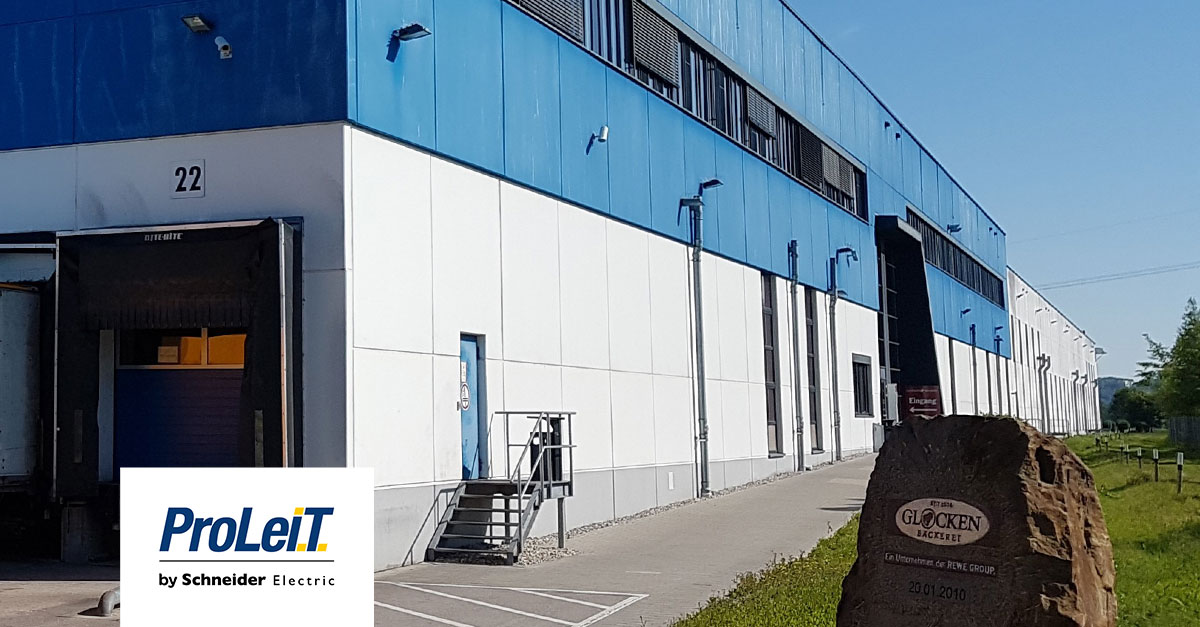
Glocken Bäckerei
The long-established Glocken Bäckerei has opted to upgrade its control system, manufacturing execution system (MES) and energy management to the latest version of Plant iT from ProLeiT.
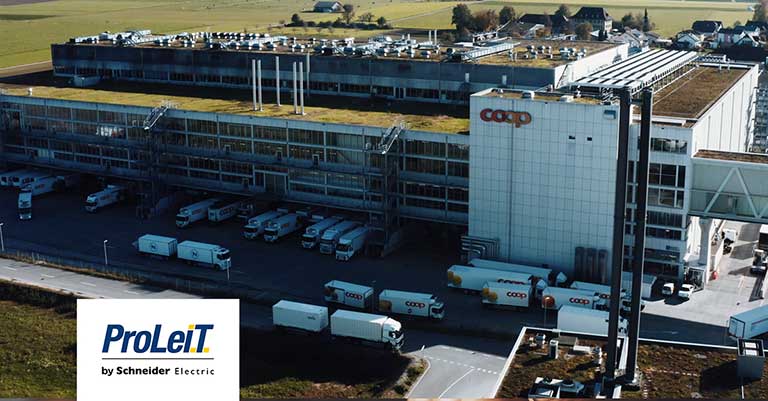
Coop
Find out more about our customer project at coop - the largest bakery in Switzerland. Thomas Meierhans and Frank Mauer discuss the general conditions, challenges and successes of this extensive collaboration.
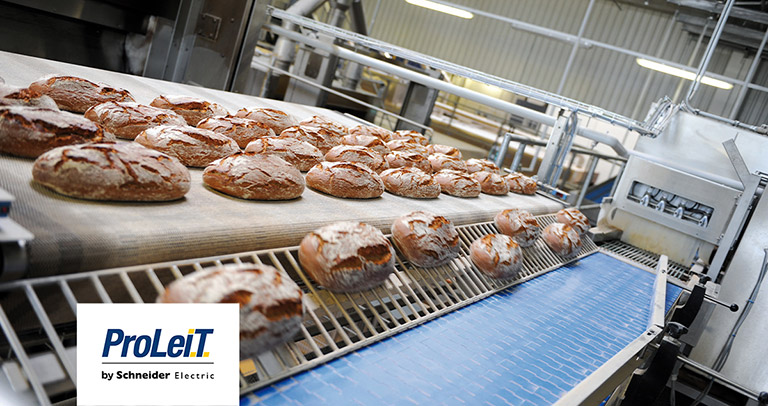
Glocken Bäckerei
Whether MES, maintenance or energy management: the more granular the data collected, the more precise the decisions that can be made on this foundation. This is demonstrated by the expanded utilization of Plant iT software at Glocken Bäckerei.
Our customers
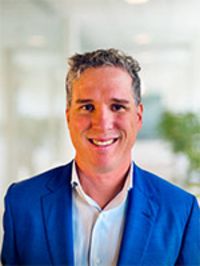
Your contact for the baked goods production of the future
Luis Soares
Branch Leader Dairy & Food
E-mail: proleitsales.request(at)se.com
Plant iT - the automation solution for the baking industry
We understand the needs of industrial bakeries. Plant iT encompasses the entire production process: from raw material delivery and storage, through recipe-controlled dough production, kneader integration, dough dividing, fermenting, resting and the baking and freezing stage to packaging and dispatching.
This industry-specific feature, coupled with cutting-edge information technology, facilitates data transparency from operational to planning levels and across all stages of value creation.
Current product highlights
In cooperation with customers, machine suppliers and renowned research institutes, our research and development team continually works on expanding and enhancing our product portfolio.
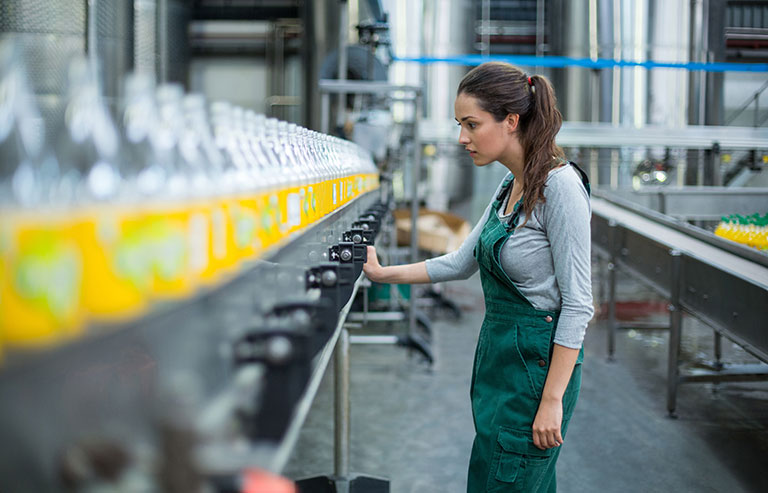
Line Management System
Minimizing downtime and maximizing plant efficiency - our Plant Acquis iT LMS add-on automatically, reliably and precisely records plant and machine downtime and ensures easy entry into the world of line management.
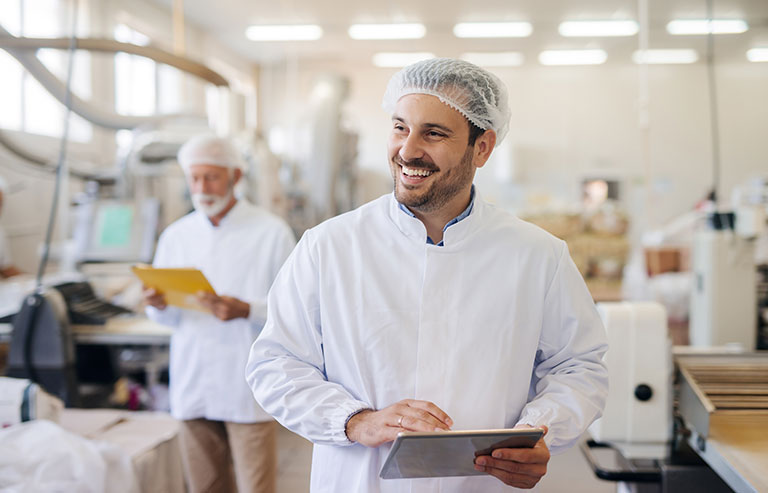
Batch Orchestration
The Plant iT Batch Orchestration System (BOS) facilitates the management, monitoring and control of batch processes. It offers a wide range of options for interacting with running orders: Recipes can be dynamically optimized, expanded and standardized at any time.
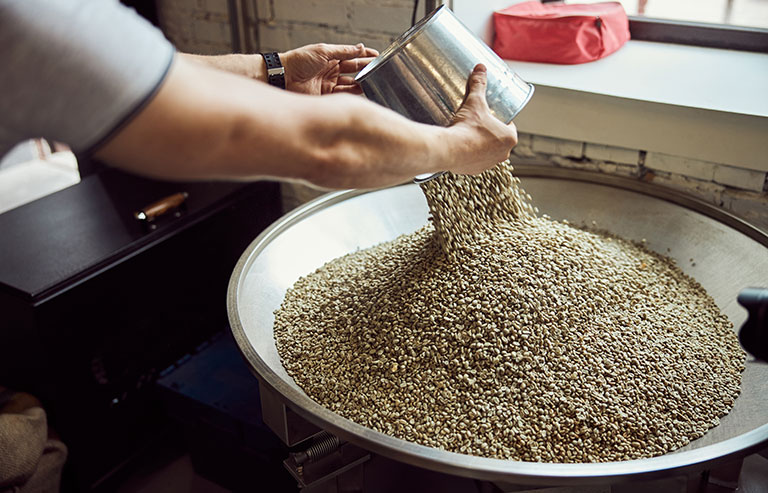
Weighing Assistant
ProLeiT's Manual Weighing System (MWS) serves as an intelligent weighing assistant, ensuring the clear processing of bills of material by visually and reliably guiding operators through the weighing process.
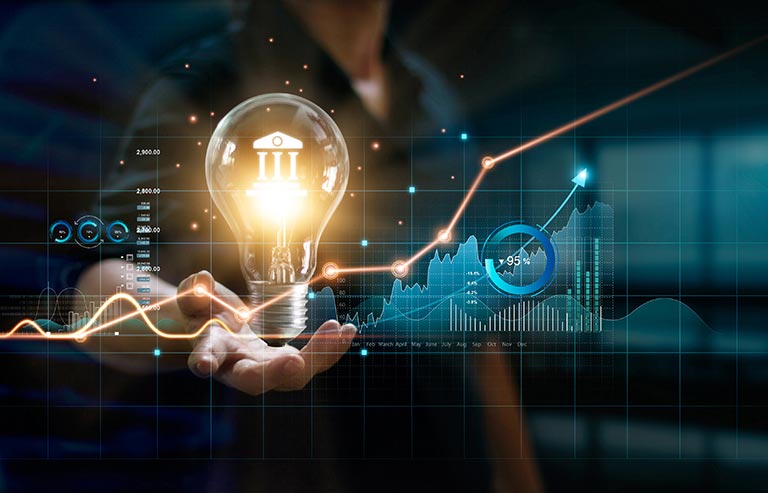
Energy Management
Efficiently monitor and control energy consumption in your plant with our Energy Management system. Identify optimization potential and improve the long-term energy efficiency of your bakery.
Take a look at the many added values Plant iT offers
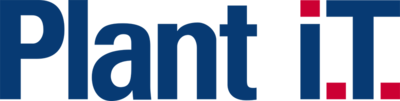
Plant iT is the modular process control system from ProLeiT GmbH and has been deployed throughout the process engineering industry in more than 110 countries for over 37 years. From operating data acquisition, process control technology, liquid handling and batch systems to functions for complete, location-independent production management (MES) and integration of ERP, LIMS and maintenance systems – Plant iT enables continuous control and monitoring of all these processes.
Thanks to a central engineering environment and optional modules, Plant iT can be expanded flexibly to meet various needs. Plant iT complies with the principle of "parameterization instead of programming". This means that individual programming is essentially replaced by the parameterization of technical and technological functions. Plant iT's system architecture offers maximum flexibility for changes, even during production, without the need to shut down operations. This time-saving approach offers our customers a distinct competitive advantage.